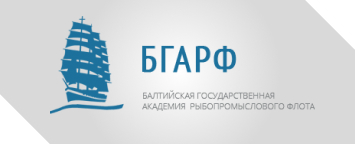
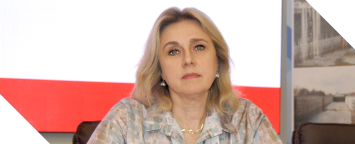
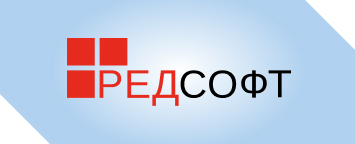
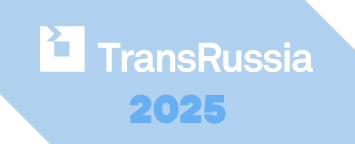
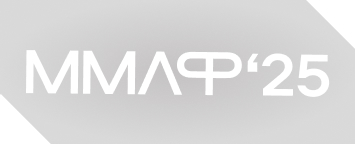
Ваш город Санкт-Петербург?
Склад при производстве нашего клиента, «Московской Пивоваренной Компании», без преувеличений, можно назвать высокотехнологичным. Компания эффективно автоматизировала большинство процессов и операций с использованием различных технологий, включая систему Solvo.WMS, которая организует работу склада и интегрируется с другими системами и оборудованием. В этой статье разберем, как компания задействует возможности автоматического размещения товаров в зоне хранения и какие преимущества это дает.
Ранее мы рассказали, как устроена автоматизация приемки продукции от производства на примере склада «Московской Пивоваренной Компании». После приемки промаркированный товар нужно разместить на складе, а затем отгрузить для дальнейшей отправки.
Если этот процесс не автоматизирован, то персонал тратит время и усилия для поиска свободной ячейки подходящего размера. Оператор с грузом вынужден ездить по складу, чтобы разместить очередную партию груза, а затем записать его место и внести эти данные в систему учета. Все это увеличивает время на выполнение складских операций и снижает эффективность. Следствием могут быть скопления неразмещенных палет, потеря грузов, путаница в системе учета, если информация о месте размещения груза была записана неверно. Неоптимальное планирование размещения грузов влечет за собой ситуации, когда небольшой по размеру груз занимает крупную ячейку, которая пригодилась бы для палеты, большей по размерам. Неэффективные действия в зоне хранения приводят к чрезмерному штивованию, увеличению персонала на смене, удлинению времени работы погрузочного оборудования и его износу.
Для решения этой проблемы в системе Solvo.WMS создаются правила и стратегии управления операциями по размещению товаров в зоне хранения склада. При размещении учитывается множество самых различных параметров – от типа и весо-габаритных характеристик груза до планируемых сроков его отгрузки и пожеланий клиента к хранению товара. Система учитывает такие характеристики груза как тип упаковки, вес и размер, требования к соблюдению температурных режимов при хранении, совместимости товаров, остаточным срокам годности, и др. Solvo.WMS ведет учет зоны хранения и предлагает наиболее оптимальную ячейку для груза, принимая в расчет сроки его дальнейшей отправки. Например, если груз должен быть отправлен в ближайшее время, то Solvo.WMS предложит такое место для размещения, откуда палету будет удобно взять, не перемещая другие. Погрузчику тоже будет предложен оптимизированный маршрут к ячейке хранения. Например, после доставки одного груза на хранение он может забрать расположенный неподалеку груз на отправку.
Кроме этого, система интегрируется с практически с любыми другими цифровыми сервисами, автоматическим и полуавтоматическим складским оборудованием (погрузчиками, конвейерными линиями, роботизированным оборудованием и пр.), выдает оптимальные задания для персонала. Все это увеличивает скорость работы и снижает риски ошибочных действий.
В 2018 году «Московская Пивоваренная Компания» модернизировала склады и перешла от штабельного хранения (это самая популярная форма на пивоваренных производствах) к узкопроходной технологии. Чтобы новая система хранения работала с максимальной эффективностью, нужно было поменять и процесс размещения продукции. В частности, теперь конвейеры подают груз от линий производства к аллеям, затем развозкой и инвентаризацией занимаются полуавтоматические и автоматический штабелеры под контролем операторов. А система Solvo.WMS контролирует и организует этот процесс.
Из-за специфики пространства было невозможно соединить линию производства с конвейером напрямую, поэтому решением задачи стало перемещение палет с помощью двухпалетных погрузчиков. Когда груз принят и оклеен штрихкодом, система формирует задание водителю погрузчика.
Далее груз размещается по алгоритму:
Solvo.WMS, получив информацию о движении груза, передает конвейеру «адрес» назначения каждой палеты. Отметим, что одна из особенностей Solvo.WMS – способность интегрироваться со сторонним ПО, которое уже используется на складе: в этом случае – с конвейерной системой. Таким образом, системы обмениваются информацией без участия оператора.
Палета проходит проверку на корректность штрихкода и соответствия габаритным характеристикам с помощью датчиков и рамок отбраковки. Если конвейерная система выявляет проблему, то палета отставляется в сторону и помечается для дальнейшего решения проблемы оператором склада.
Когда груз доставлен по конвейеру в транзитную зону к нужной аллее, оператор узкопроходного штабелера получает задание на погрузку. Он физически перевозит палету по проходам к нужной ячейке. Solvo.WMS получает от системы конвейера уведомление о том, что груз на месте, и помечает ячейку как занятую.
Если поблизости есть груз, назначенный на отбор, то оператор штабелера получит задание забрать его.
Solvo.WMS назначает места для грузов в соответствии с заданными правилами и стратегиями. Например, она распределяет продукцию по аллеям равномерно. Такая стратегия позволяет задействовать одновременно все штабелеры и все проходы, если поступит запрос на большой объем однотипной продукции: машины не будут сталкиваться и смогут оперативно отгрузить требуемый объем.
Еще одна важная стратегия – ориентироваться на остаточный срок годности продукции. Это также важно для своевременной отгрузки.
Система Solvo.WMS интегрирована с полуавтоматическими и автоматическим штабелерами. Она может передавать «адрес» ячейки на штабелер, чтобы он подъезжал к нужному месту. Вне зависимости от «водительского стажа» оператора техника будет двигаться с оптимальной для нее скоростью.
Благодаря этой интеграции удалось также автоматизировать инвентаризацию на складе. На штабелер устанавливается специальная камера, направленная на стеллажи по обе стороны от машины. Штабелер двигается со своей обычной скоростью и одновременно сканирует коды ячеек и штрихкоды палет. Solvo.WMS мгновенно проводит сверку и выдает задание на ручную инвентаризацию только спорных случаев.